Commercial Roof Replacement Services
Comet Roofing Contractors emphasizes quality, safety, and transparency in their roofing projects. Replacing a commercial roof is a major decision that requires careful evaluation. The team consists of highly trained and licensed professionals who are committed to providing exceptional results. With an adequately staffed crew and a well-defined process, they ensure timely, consistent, and reliable service.
In the process of commercial roof replacement, certified contractors at Comet Roofing specialize in various roofing systems, including metal standing seam, TPO membrane, and modified bitumen. Their comprehensive approach includes conducting thorough inspections of the roof deck, ensuring proper installation of flashing, and complying with relevant building codes.
Each commercial roof replacement starts with a detailed assessment to uncover potential issues such as water infiltration or structural damage. The use of premium underlayment materials and industry-leading sealants helps ensure durability against severe weather. Project managers oversee every phase of the roof replacement, coordinating closely with building managers to minimize disruption to business operations while upholding the highest standards of waterproofing and insulation solutions.
Four Main Material Categories for Commercial Roofing
Single-Ply Commercial Roof Installation
Installing single-ply commercial roofing entails a series of essential steps designed to enhance durability and performance under various weather conditions. The process begins with the preparation of the roof deck, where professional roofers ensure that it is clean, dry, and free of any debris that might impact the roofing system's integrity. This preparation may involve power washing, addressing ponding issues, and repairing any structural weaknesses in the substrate.
Following deck preparation, a robust rigid insulation layer is installed. This layer not only provides thermal protection and energy efficiency but also contributes to the structural stability of the roofing system by minimizing thermal bridging, which can lead to condensation and diminish the R-value performance.
After the insulation is in place, the next step involves carefully laying the single-ply membrane—such as TPO, PVC, or EPDM rubber—over the insulation. Proper alignment and sufficient overlaps at the seams are critical during this phase to ensure the longevity of the roofing system and to avert potential issues like billowing or premature failure.
The method of attachment for the single-ply membrane varies depending on the specific building requirements and regional weather conditions. There are several techniques, including the use of specialized adhesives for fully-adhered systems, precision-placed mechanical fasteners to enhance wind uplift resistance, or ballast methods utilizing river rock or pavers for inverted roof membrane assemblies (IRMA).
To ensure watertight integrity, qualified installers will weld or seal all seams. Hot-air welding is commonly applied to thermoplastic materials like TPO and PVC, creating strong molecular bonds. In contrast, EPDM roofing often requires specialized seam tape or liquid adhesives to achieve the necessary seal integrity.
Detail work is a vital aspect of quality single-ply roofing installations. This includes careful flashing around areas such as roof perimeters, HVAC curbs, vents, drains, and other penetrations—points that are particularly vulnerable to water infiltration.
Finally, a thorough quality control inspection is performed, often employing electronic leak detection methods to verify the waterproof integrity of the new roofing membrane. This systematic approach ensures optimal performance and prolongs the service life of the commercial roofing installation.
Bitumen Commercial Roof Replacement
Begin by preparing the roof deck, ensuring it is clean, smooth, and free of debris. This essential initial step in bitumen commercial roofing involves a thorough inspection for structural integrity and effective drainage. Local commercial roofers often recommend power-washing the surface to eliminate any contaminants that could hinder adhesion. After adequately prepping the substrate, install a base layer, usually an insulation board, for increased stability and thermal protection.
The success of quality bitumen commercial roofing hinges on proper insulation selection—polyisocyanurate or high-density fiberboard are the industry standards, delivering excellent R-value. Carefully roll out the modified bitumen sheets, ensuring they are aligned properly. These sheets can be applied using torch-down, cold adhesive, or self-adhesive techniques. Many local commercial roofers opt for the torch-down method for bitumen roofing, especially in changing weather conditions.
To create a watertight seal, overlap seams and secure them using heat or adhesive. For top-tier bitumen commercial roofing installations, maintain consistent 6-inch side laps and 8-inch end laps, applying uniform pressure with a weighted roller to eliminate air pockets. Flashing should be installed around edges and roof penetrations for extra protection, using reinforced membrane flashing compatible with your bitumen commercial roofing setup.
Counter-flashing must be mechanically fastened and sealed with elastomeric mastic to enhance water resistance. Finish the installation with a cap sheet for added durability and a comprehensive inspection. The cap sheet in bitumen commercial roofing often features ceramic granules or reflective coatings to guard against UV degradation and ensure a Class A fire rating. Be sure to apply bitumen commercial roofing mastic at all termination points and around roof protrusions such as vents, HVAC curbs, and drainage systems.
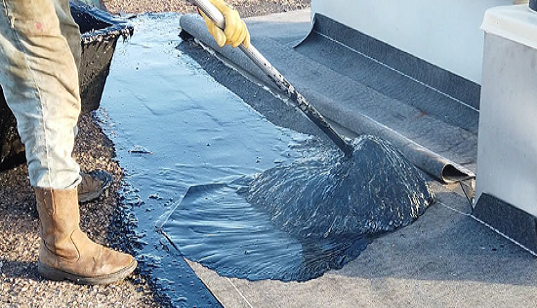
Built-Up (Tar) Commercial Roof Replacement
Installing a built-up tar commercial roofing (BUR) system involves layering various materials to create a long-lasting, weather-resistant surface that withstands harsh conditions over time. Professional commercial roofers in my area recommend starting with a comprehensive deck inspection to verify structural integrity before applying any materials. The substrate must be clean, dry, and free of debris to ensure optimal adhesion when installing built-up tar roofing systems.
Begin by applying a base layer of insulation or felt to improve stability and energy efficiency, forming a thermal barrier that helps lower heating and cooling costs throughout the building's lifespan. Top-quality polyisocyanurate or rigid foam insulation boards deliver excellent R-values for commercial applications. Alternating layers of hot asphalt (or tar) and roofing felt are then applied, creating a watertight bond that prevents moisture intrusion and potential leaks. The bitumen in built-up tar commercial roofing serves both as an adhesive and a waterproofing agent, forming a seamless membrane across the roof.
Typically, three to five layers are applied, depending on the desired durability and specification needs. Each ply strengthens the built-up tar commercial roofing system, enhancing its tensile strength and puncture resistance. Skilled commercial roofers I can find nearby use specialized equipment, including hot kettles, felt layers, and propane torches, to ensure the correct application temperatures for ideal adhesion between layers.
Finish the roofing project with a protective cap sheet or gravel ballast to guard against UV rays and weather damage. The aggregate surface of built-up tar commercial roofing offers excellent fire resistance and extends service life by reducing photochemical degradation. To enhance reflective qualities, some building owners opt for a modified cap sheet featuring factory-applied mineral granules instead of traditional gravel surfacing.
Conduct a detailed inspection to confirm proper sealing and alignment, paying close attention to flashing details around roof penetrations, parapet walls, and drainage systems. Quality built-up tar commercial roofing installations incorporate appropriate edge metal terminations and expansion joints to handle building movement and thermal cycling without compromising the waterproofing integrity.
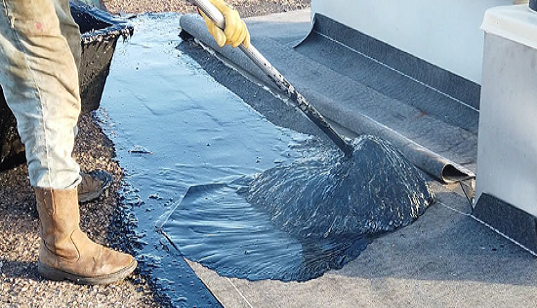
Metal Commercial Roof Replacement
Installing a metal commercial roofing system requires careful attention to detail and strict compliance with roofing industry standards. The durability and effectiveness of your metal commercial roofing investment are significantly influenced by accurate installation practices. Commercial roofers trained specifically in metal roof systems recognize that precision is essential when working on these high-performance roofing solutions.
Begin with a thorough inspection and preparation of the existing roof deck, making sure it is clear of debris, moisture, and any structural issues. Professional commercial roofers will ensure that the substrate meets load-bearing requirements before applying any metal commercial roofing. The deck must be structurally sound to handle the weight of the metal roofing system and endure environmental stressors such as wind uplift and snow loads.
Next, install a top-quality waterproof underlayment—this vital moisture barrier serves as essential secondary protection beneath your metal roofing. Premium synthetic underlayments designed for metal commercial roofing applications provide enhanced tear resistance and longevity compared to traditional felt products. This layer establishes a watertight foundation while allowing for thermal movement that is characteristic of metal roofing systems.
When arranging metal panels or standing seam profiles, skilled contractors always begin at the roof's eave edge and methodically work upward toward the ridge. Proper panel overlap is crucial in metal commercial roofing to create secure seams that prevent water leaks. Fasten each panel using the appropriate fastening systems—either exposed fasteners with neoprene washers or concealed clip systems based on the selected metal roofing profile.
Installing custom-fabricated flashing around roof penetrations, valleys, and transitions is one of the most intricate aspects of metal commercial roofing. Proper installation of drip edges, rake flashing, and counterflashing protects susceptible areas from moisture infiltration. Ridge caps and hip covers not only enhance the visual appeal but also provide essential weatherproofing at these high-exposure points.
Once the installation is complete, a thorough inspection of the entire metal commercial roofing system should confirm correct panel alignment, secure attachment, and watertight integrity—ensuring that your building benefits from decades of reliable performance from its premium metal commercial roofing investment.